WEISSER EMO exhibits from the turning and milling sector
Powerful machining centers and demanding applications
At this year’s EMO, the Hardinge Group will be presenting a wealth of technical innovations in the field of turning and milling.
WEISSER will be presenting two trade fair innovations, among others: A 5-axis horizontal machining center, the MultiCenter MTS 1200/8, and a manufacturing solution for machining and coating brake discs of the latest generation with the LMD BD 450 laser coating system.
WEISSER MultiCenter MTS 1200/8
The multifunctional, horizontal machining center WEISSER MultiCenter MTS 1200/8, presented for the first time at the EMO, is predestined for the complete machining of highly complex and precise workpieces from the fields of mechanical engineering, electromobility, medical technology and the aerospace industry.

The newly developed machining center WEISSER MultiCenter MTS 1200/8 with integrated automation
The focus of the design was on maximum flexibility and user-friendliness, in addition to the best possible precision and vibration damping. The solidly designed basic mechanics in combination with 55 mm guides guarantee the best performance for demanding applications in hard and soft machining. The 600 mm X-stroke of the milling unit facilitates the use of long tools of 330 mm length. Compared to similar machine tools, the engagement depth of only 480 mm is significantly lower and ensures ergonomic access to the working area. The extra wide viewing window provides the necessary overview into the machine.
Thanks to the high degree of technology integration, there are virtually no limits to the machining spectrum. This ranges, for example, from highly complex hydraulic components to tool holders, sophisticated shafts and e-mobility components.
In addition to classic turning, milling and drilling, the machining center can also map the process technologies of rotary turning, hob peeling, gear hobbing and whirl turning. Optionally, the machine can also be equipped with a laser head for additive manufacturing.
With regard to workpiece handling, the MultiCenter MTS 1200/8 optionally offers an interesting alternative to the usually cost-intensive, external loading and unloading gantries or space-consuming robot cells. For workpieces with a maximum diameter of 160 mm and a maximum workpiece weight of 20 kg, the machining center can be optionally equipped with integrated automation. The integrated loading and unloading handling system can approach both spindle noses via NC axis and remove the workpieces by means of one gripper each for the main and counter spindle. The starting position from which the workpiece or residual piece is removed or deposited is located on the right-hand side, outside the machine tool.
Weisser LMD BD 450
DSince the Euro 7 standard also regulates brake abrasion, the coating of brake discs is moving into the focus of manufacturers, because new technologies can transform conventional brake discs into wear-reduced and corrosion-resistant “low-emission break discs”. As a specialist for brake disc machining, WEISSER, in addition to the previous process chain, which includes turning, drilling and grinding, will also offer the option of laser coating in the future.
For this, WEISSER relies on so-called laser cladding, also known as laser buildup welding. In this additive manufacturing process, a material powder is blown through an inert gas into the focus of a laser beam. The powdered coating material melts in the inert gas even before it hits the likewise molten surface of the workpiece, in this case the brake disc. The result is a metallurgically bonded corrosion- and abrasion-resistant hard coating on the brake disc, with low thermal distortion. This enables the complete manufacturing solution for large-scale production of the next generation of brake discs up to Ø 450 mm by means of a cost-effective cost-per-part concept.
In the process chain, turning and drilling operations are first carried out on two UNIVERTOR AM-T vertical machining centers. This is followed by laser coating in two steps, in which first the compound layer and then the carrier layer are applied. The downstream grinding process produces the required workpiece geometry.
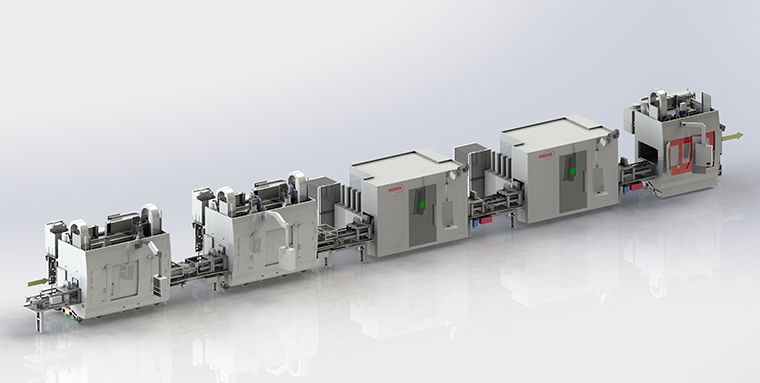
Illustration of the processing line of laser-coated brake discs of the latest generation
WEISSER UNIVERTOR V400
With the UNIVERTOR V400, WEISSER has taken proven technology a step further and expanded the well-known UNIVERTOR series.
Two powerful disc turrets in combination with a 4-axis unit enable highly productive simultaneous machining and thus shortened machining times or reduced unit costs. Due to the large A8 spindles as well as the reinforced turrets, a high machine stability is ensured, which enables the most diverse manufacturing processes with the best surface quality.
The range of applications in medium and large series production covers a wide variety of materials such as cast iron, aluminum, steel as well as titanium, from brake discs, differential housings, stator housings to axle drive wheels. The heart of the UNIVERTOR V400 is the proven WEISSER Pick-Up System. This can be combined with customized automation concepts. As standard, the UNIVERTOR V400 is equipped with a cost-effective and functional drag frame conveyor.

WEISSER UNIVERTOR V400